A Tesla owner was confronted with a $14,000 repair bill just one day after purchasing a Model Y. This incident, as detailed in a Reuters report, is indicative of broader issues that Tesla is experiencing.
The Model Y’s suspension broke with only 115 miles on the odometer, highlighting a significant concern for new owners about the reliability of their vehicles.
Initial Breakdown: Suspension Failure at 115 Miles
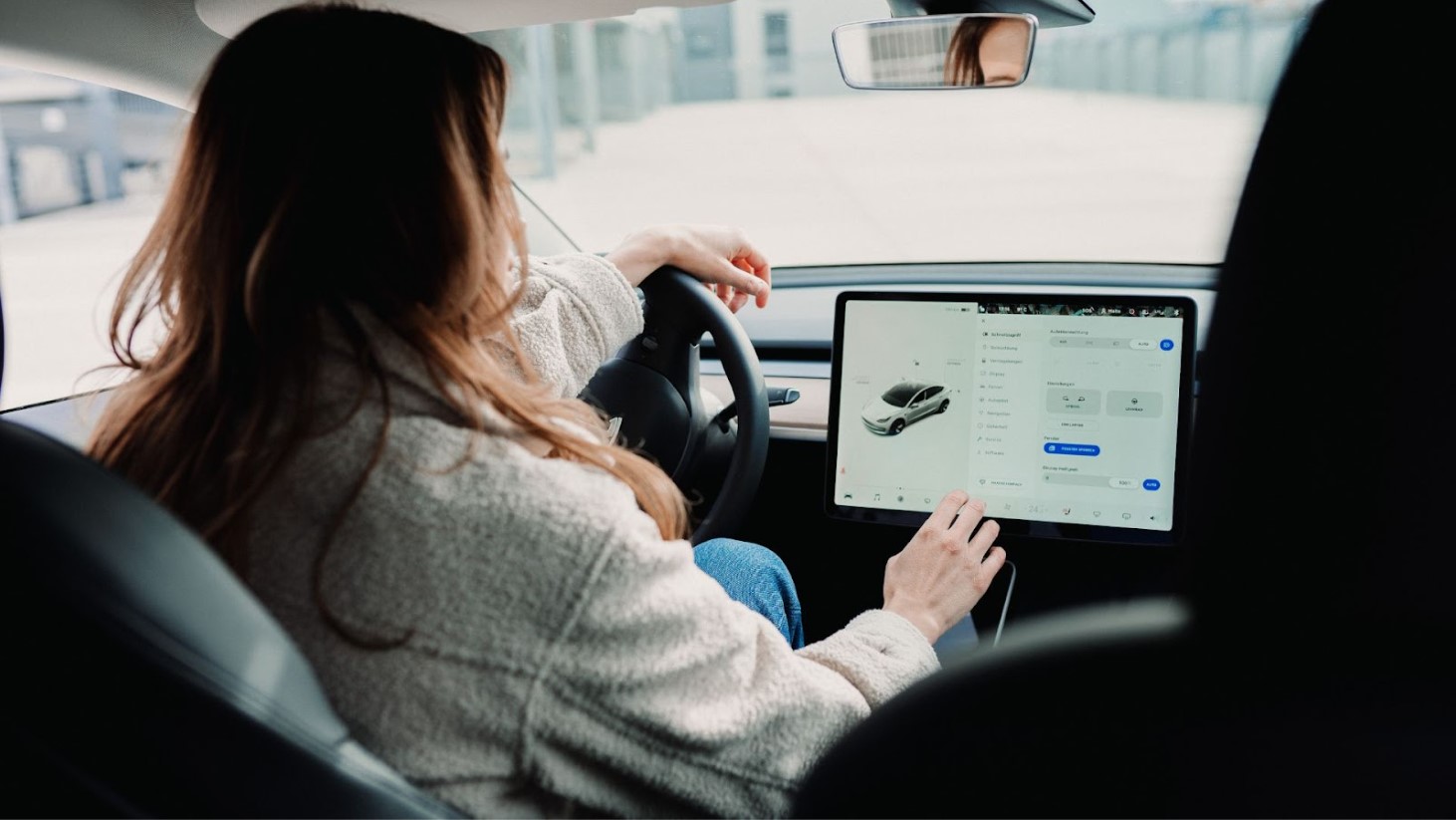
The Tesla Model Y experienced a suspension failure at a mere 115 miles, as reported by Reuters. This failure not only represents a substantial inconvenience for the owner but also raises questions about the overall build quality of Tesla vehicles.
The issue was so severe that it caused the vehicle to come into contact with the road, losing steering capabilities.
Tesla’s Wider Suspension and Steering Issues
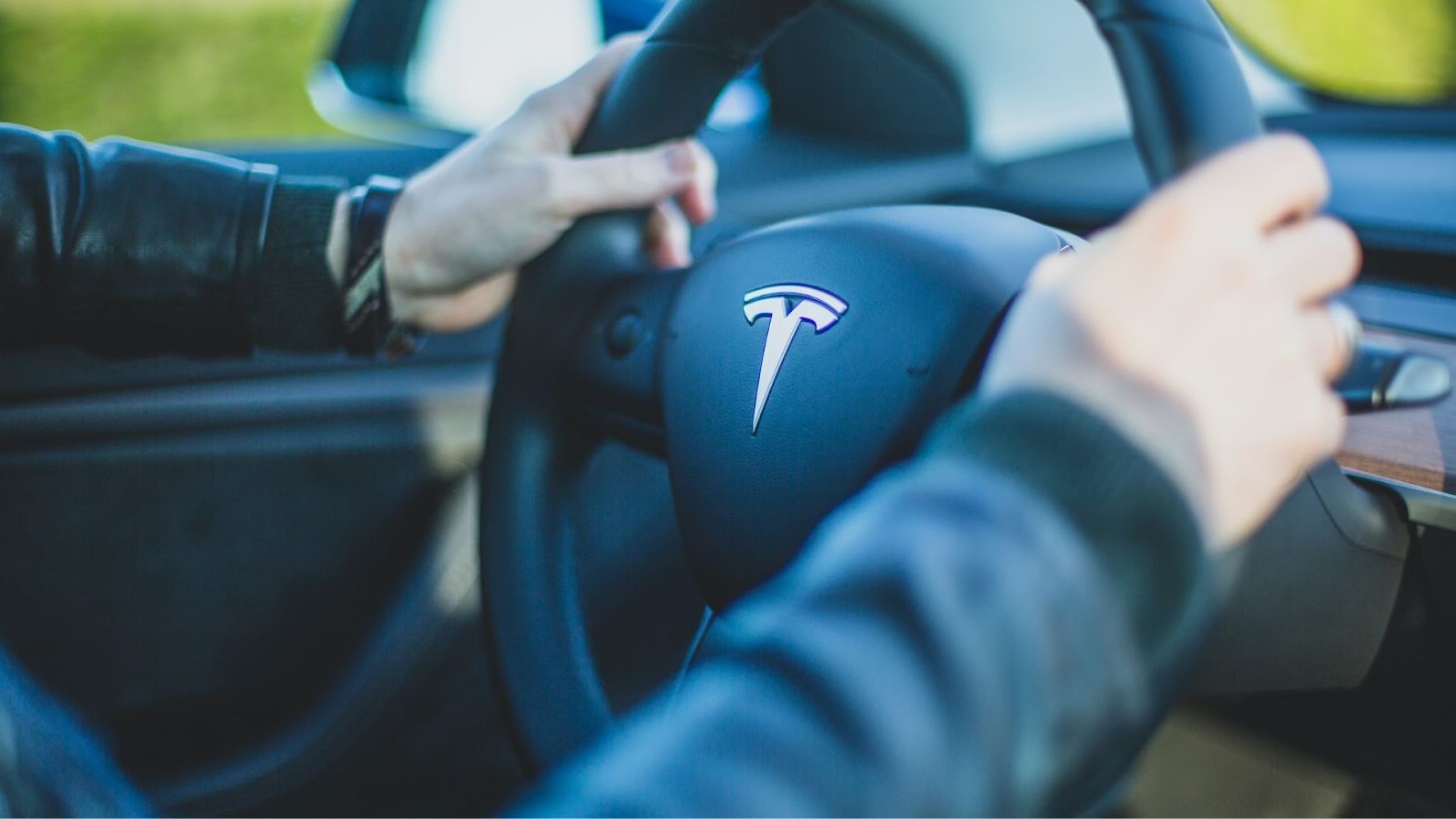
According to a comprehensive investigation by Reuters, which included interviews with over 20 customers and 9 Tesla workers, and analysis of thousands of internal documents, Tesla has received numerous complaints regarding suspension and steering over the past six years.
This pattern of complaints suggests that these issues are not isolated incidents but part of a larger systemic problem within Tesla’s manufacturing process.
Hidden Flaws: Tesla’s Internal Knowledge
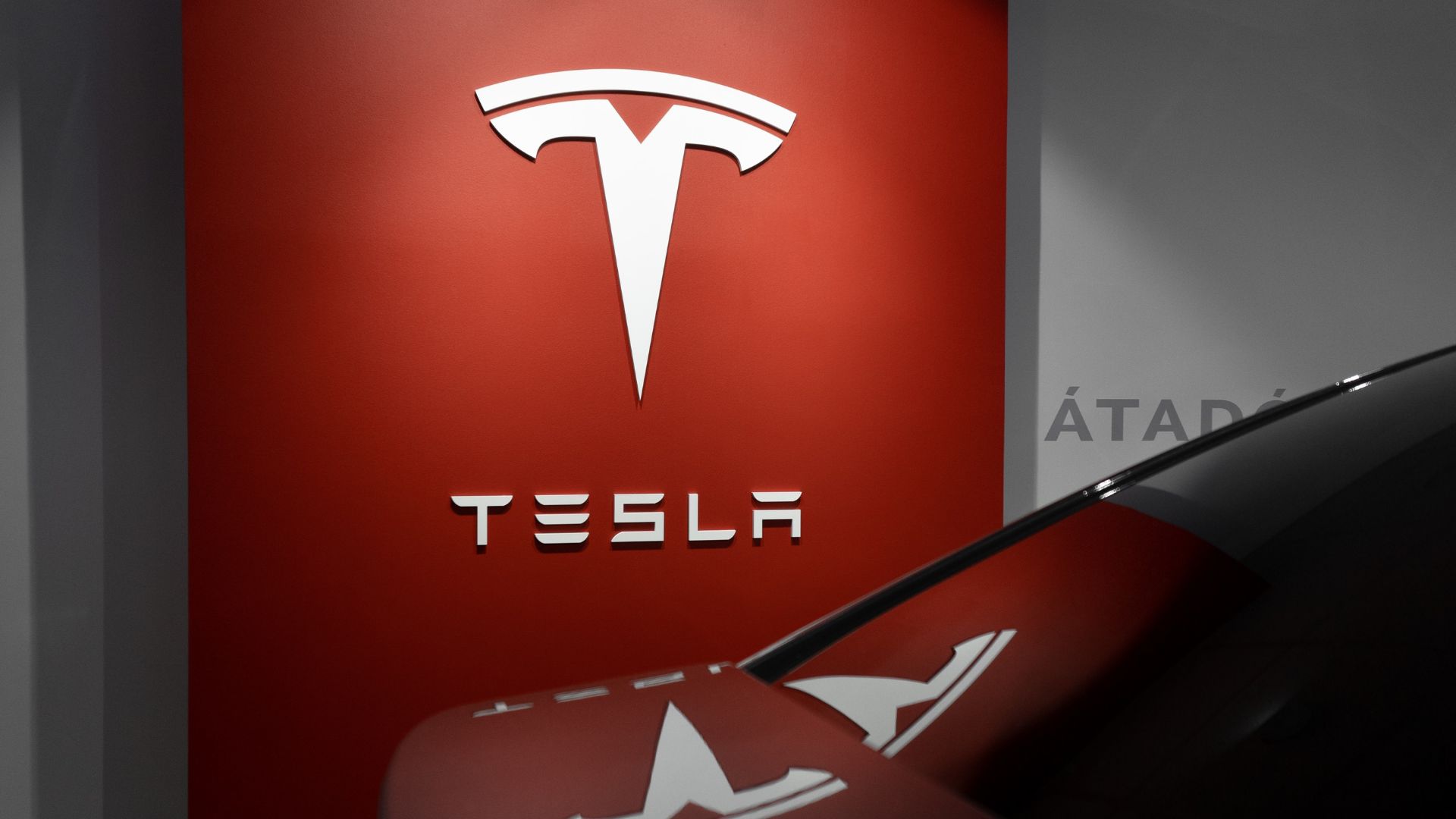
The investigation by Reuters reveals that Tesla’s internal records, dating from 2016 to 2022, paint a troubling picture. They claim the company had detailed reports and analyses on parts with high failure rates and even instructed technicians globally to inform customers that broken parts were not faulty.
One shocking instance involved a 2021 accident where a Tesla technician reported, “Front wheel fell off while driving on Autopilot at 60 mph.”
Tesla’s Response to Quality Concerns
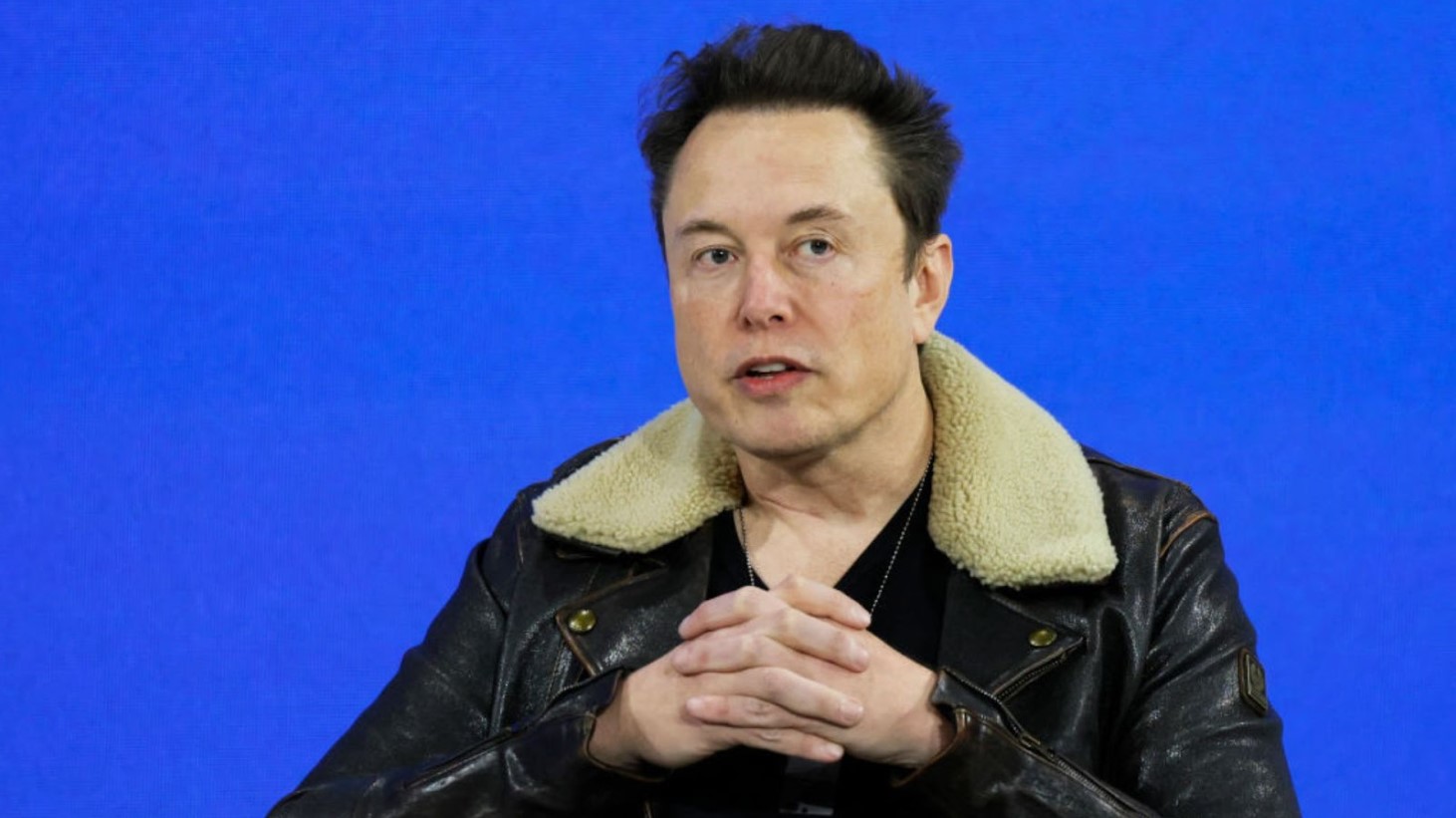
Tesla, having disbanded its press department, has not responded directly to these specific complaints. However, Elon Musk, Tesla’s CEO, acknowledged in a 2021 discussion with auto expert Sandy Munro that the company has faced quality issues, particularly during periods of increased production.
Musk stated, “When you go faster, you just discover these things,” indicating a correlation between production speed and quality control.
Musk’s Stance on Tesla’s Quality
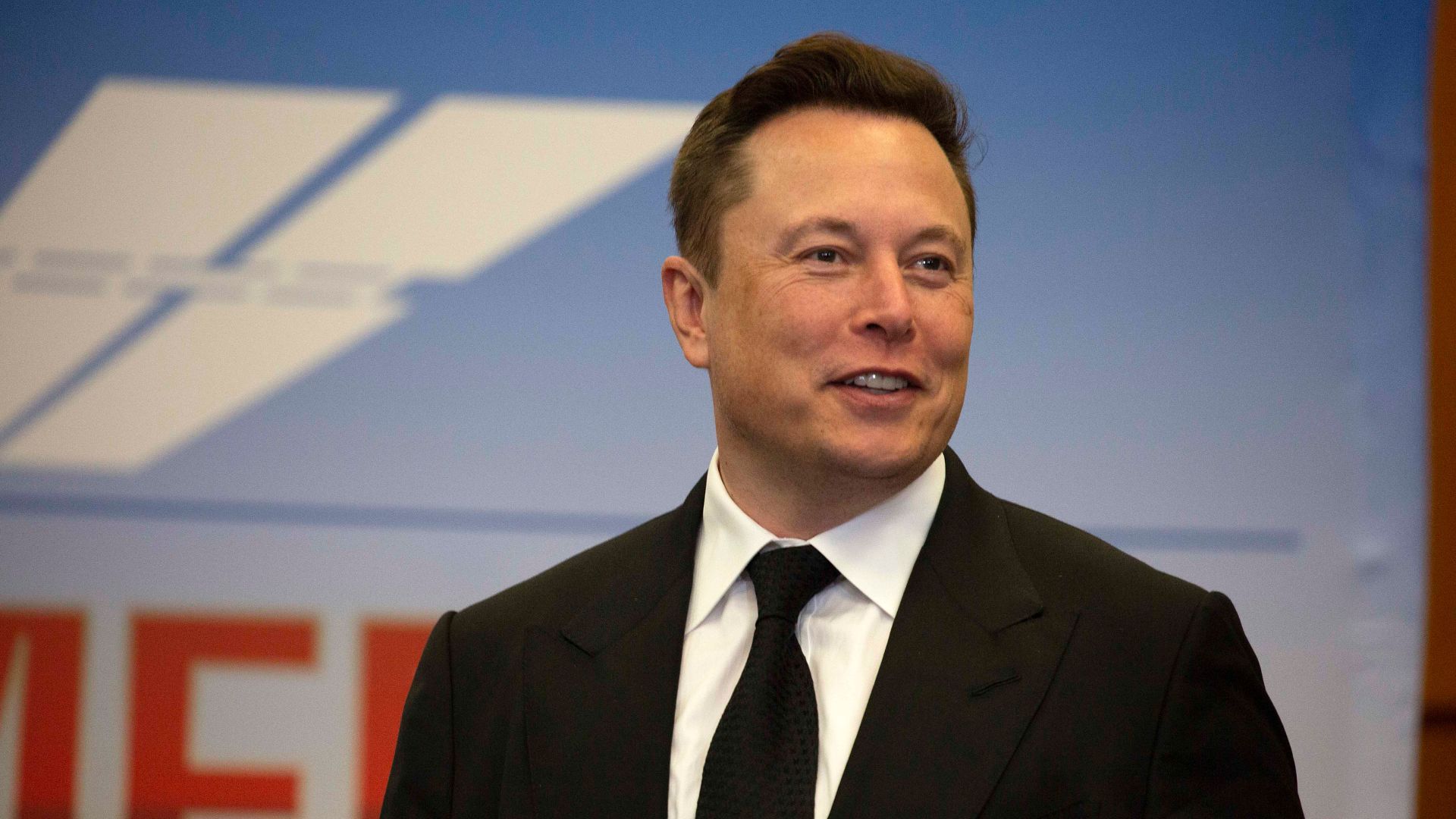
Despite these reported failures, Tesla CEO Elon Musk has maintained a positive outlook on Tesla’s quality. At a New York Times event, he asserted, “We make the best cars.”
However, the ongoing issues with Tesla’s steering and suspension components contrast sharply with Musk’s confident claims, highlighting a significant disconnect between executive perception and customer reality.
Tesla’s Strategy: Denial and Cost Shifting
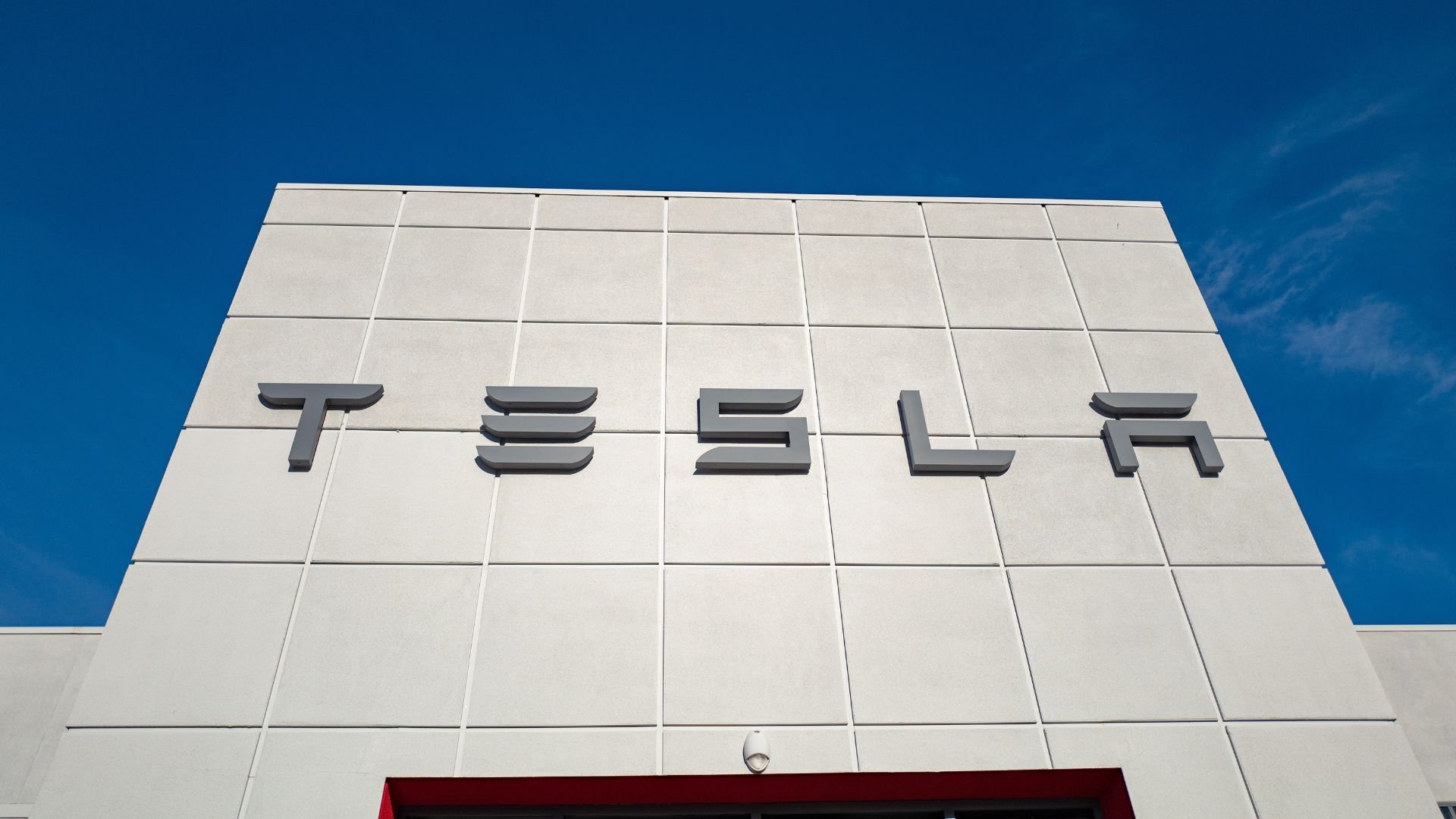
Reuters argues that Tesla’s approach to addressing these part failures has been marked by denial and shifting repair costs to customers. This strategy is evident in their responses to regulatory bodies and the public.
Despite having detailed internal records of the failures, Tesla consistently denied responsibility, often leaving customers to bear the burden of costly repairs for what appeared to be inherent vehicle flaws.
Owner’s Transition From Joy to Fear
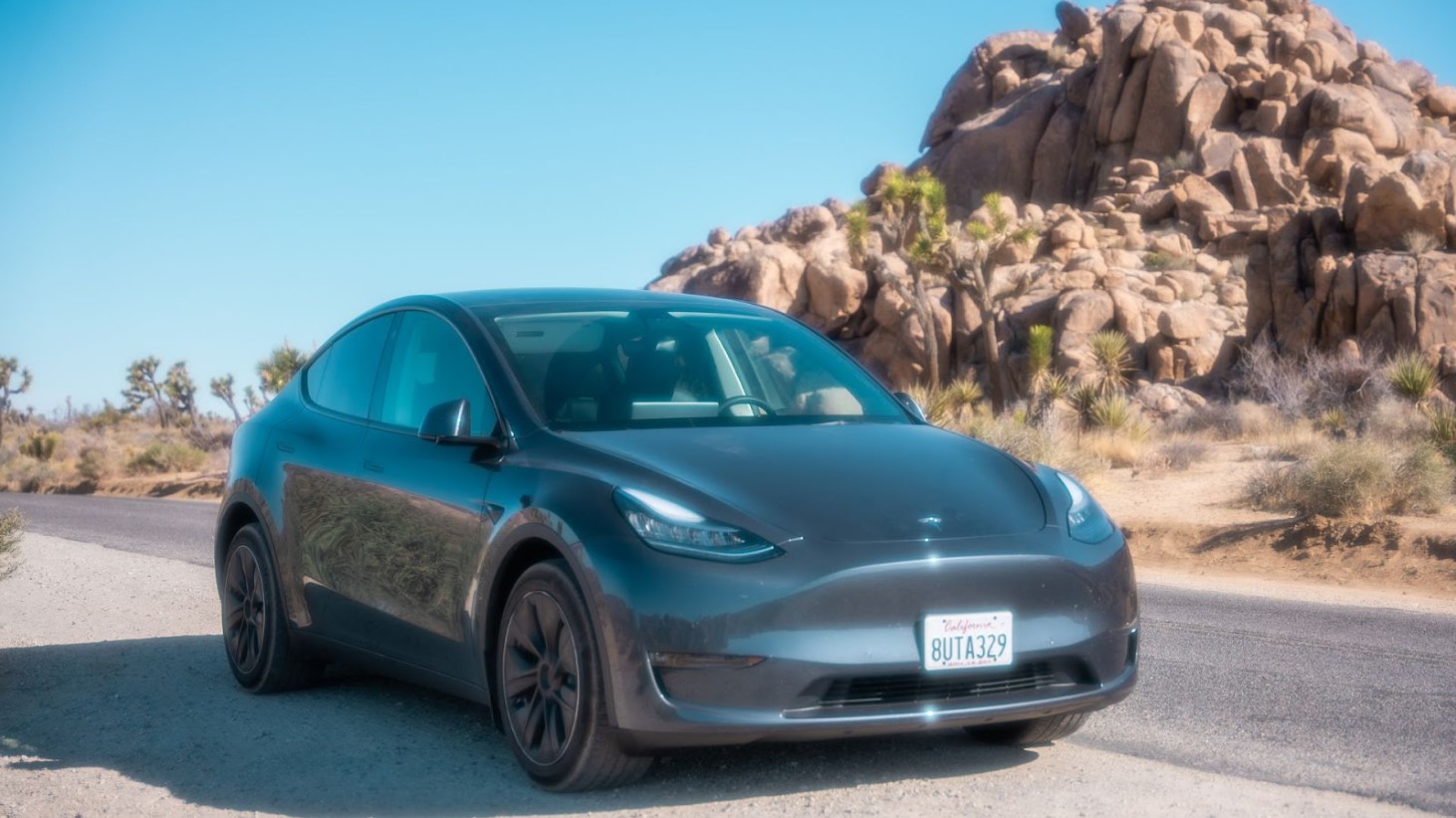
Shreyansh Jain, the former Tesla owner, described his experience to Reuters, saying his family went from “over the moon” to “absolutely petrified” when their new car broke down.
This experience illustrates the emotional impact and safety concerns that can arise from such unexpected vehicle malfunctions, particularly in newly purchased cars.
Financial Impact on the Owner
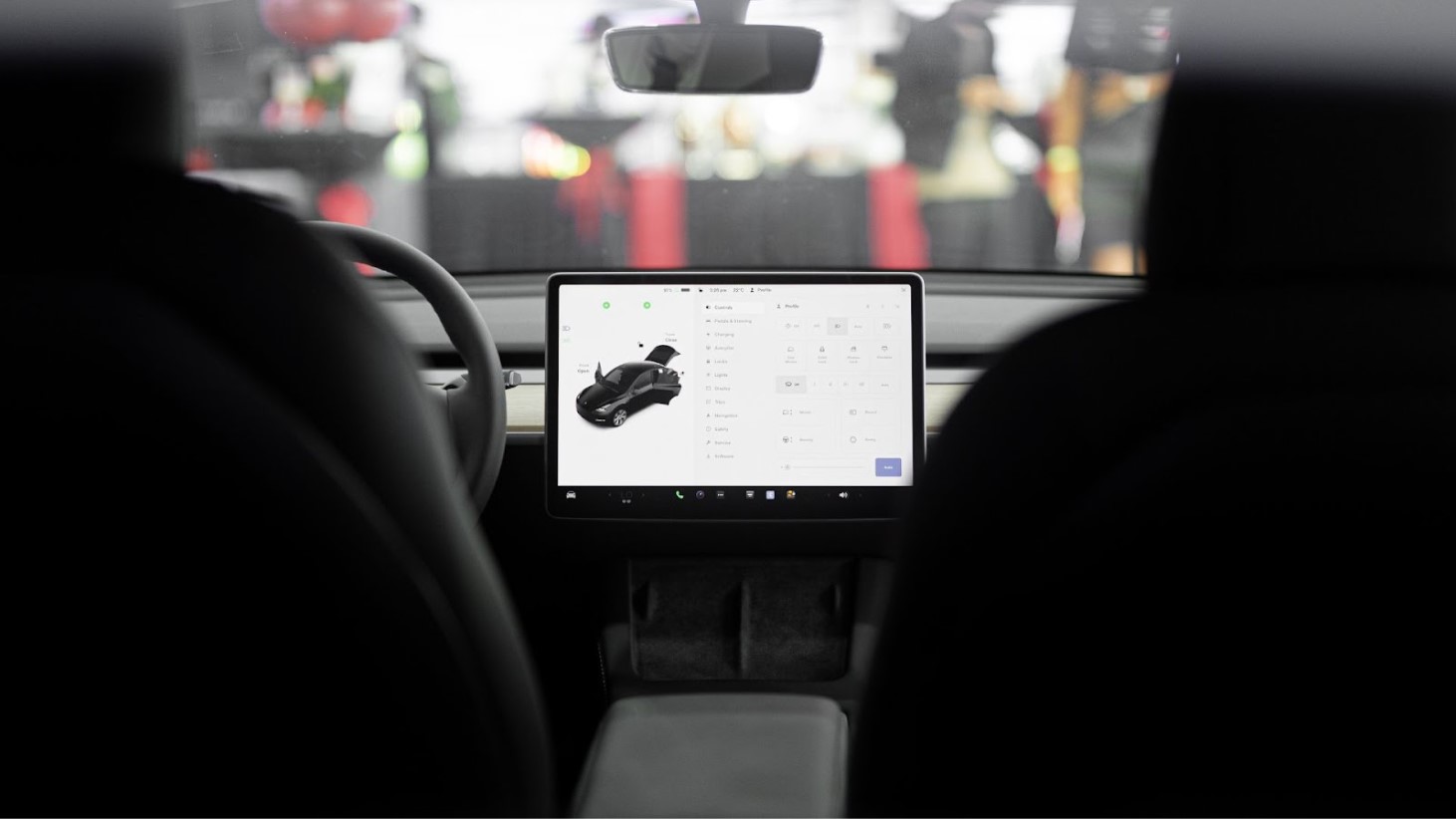
Jain was initially under the impression that Tesla would cover the repair costs, as per his conversation with Reuters.
However, he later received a letter from Tesla indicating that the $14,000 repair bill was due to “prior” damage. This situation led to increased insurance premiums for Jain and a deductible payment of approximately $1,250, adding financial strain to the already stressful situation.
The Challenge of Tesla Repairs: High Costs and Lengthy Waits
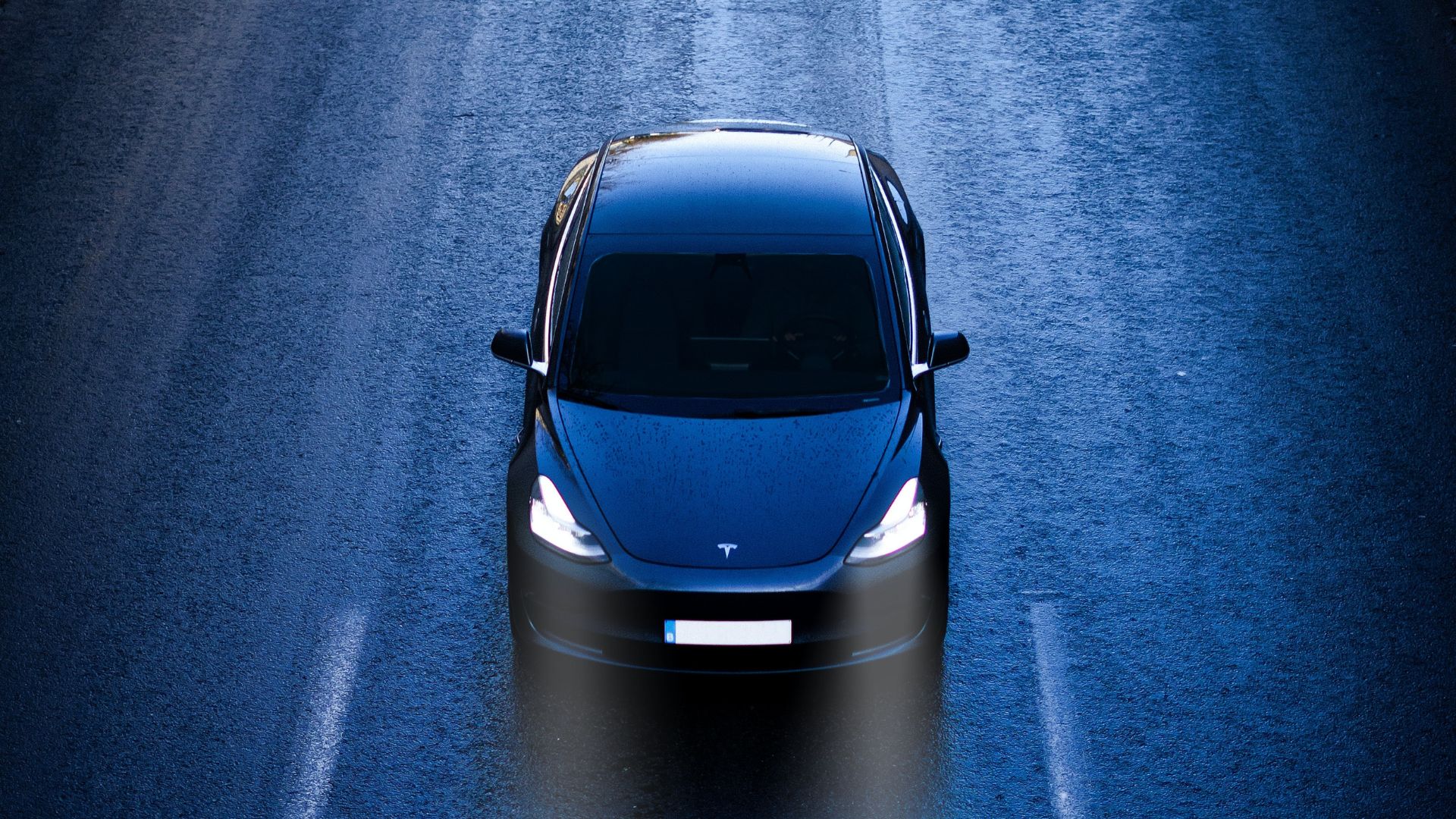
GeekWire reports on another Tesla owner who faced significant challenges when getting her car repaired. Kelly Campbell’s experience with her Tesla after a minor collision reveals a growing concern among Tesla owners.
Despite the damage appearing superficial, the repair process stretched over half a year and cost $14,000, with an additional $2,000 in car rental fees. This situation is not unique to Campbell; many Tesla owners report similar experiences of slow and expensive repairs.
Navigating the Repair Process: Parts and Insurance Delays
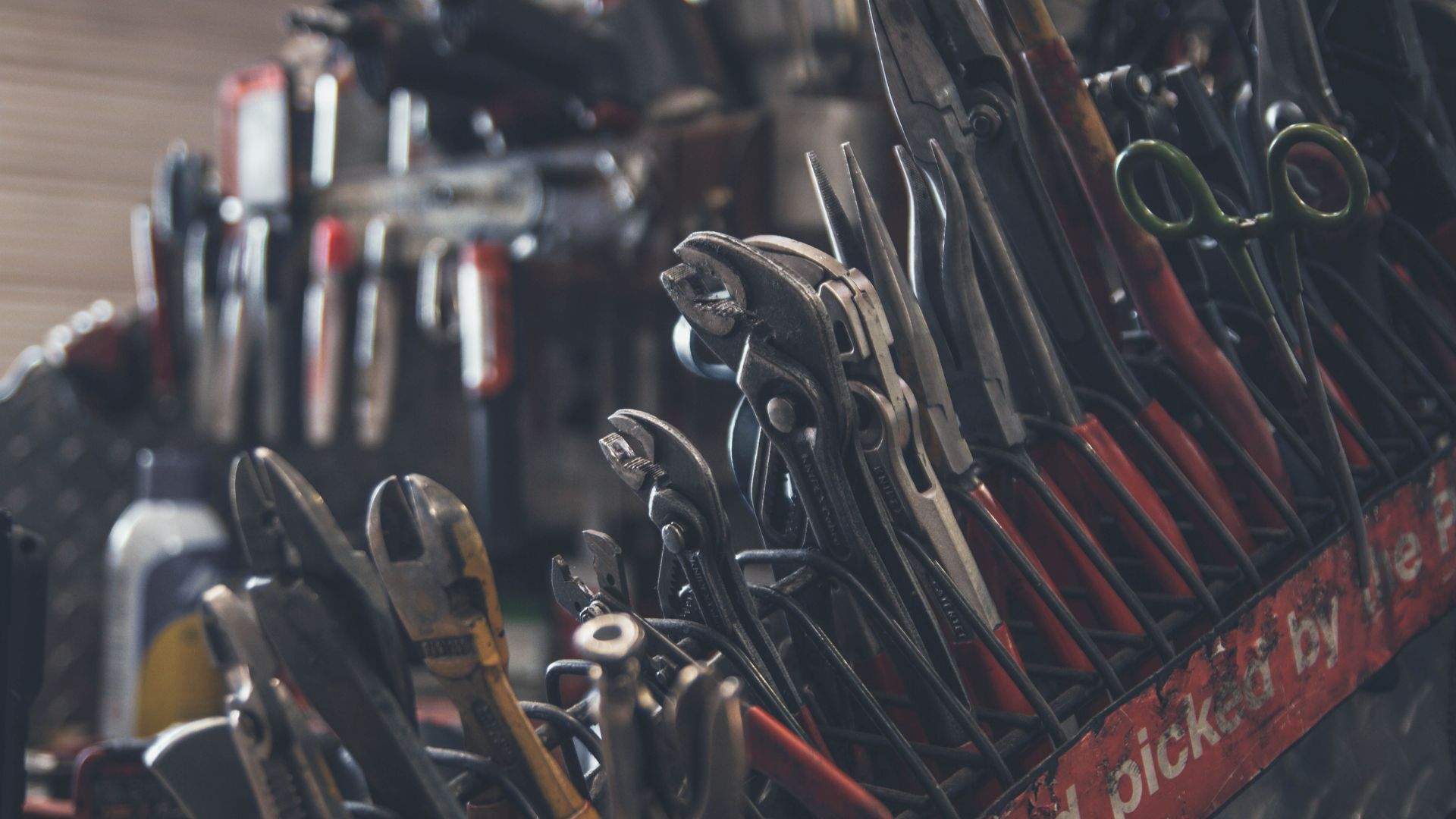
One of the primary reasons for delays in Tesla repairs is the shipping of parts from California. Tesla is reportedly setting up a parts and assembly facility in Marysville, Wash., to alleviate this issue, GeekWire reveals.
Additionally, negotiations between insurance companies and repair facilities regarding costs can further prolong the repair process.
Factors Contributing to Tesla’s Repair Expenses
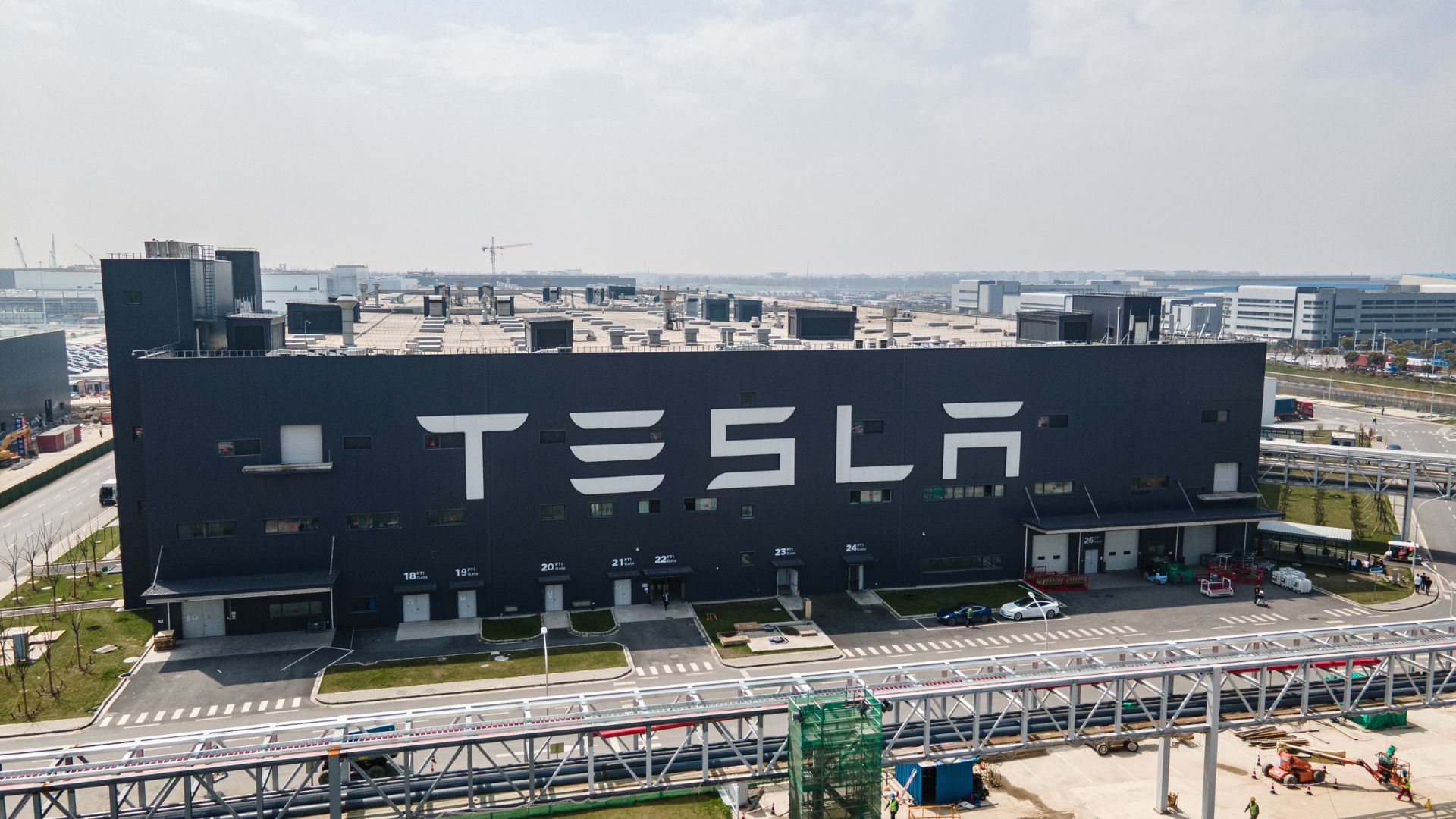
GeekWire explains there are several reasons why repairing a Tesla can be more expensive.
These include the need for Tesla-specific parts and tools, adherence to precise repair procedures, and the employment of specially trained technicians. William Parkins, general manager of Metro Auto Rebuild, explained, “The technology you know and love takes so much time to diagnose and to fix.”
Broader Quality Control Issues at Tesla
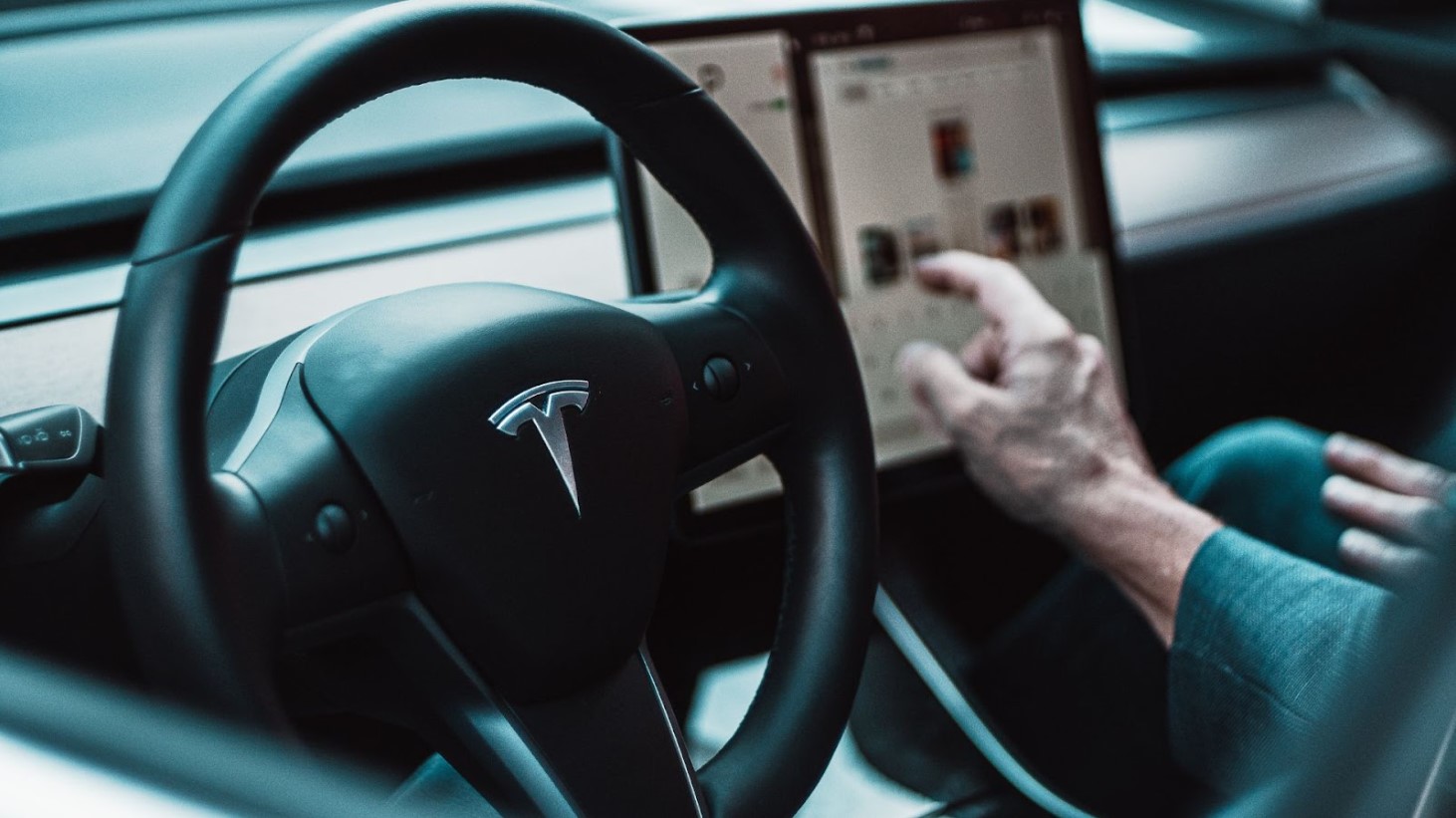
The quality control at Tesla has been a subject of scrutiny in the past.
The National Highway Traffic Safety Administration (NHTSA) investigated reports of Tesla steering wheels detaching while driving earlier this year. Such incidents raise serious concerns about the safety and reliability of Tesla vehicles.
The Role of Control Arms and Links in Tesla’s Woes
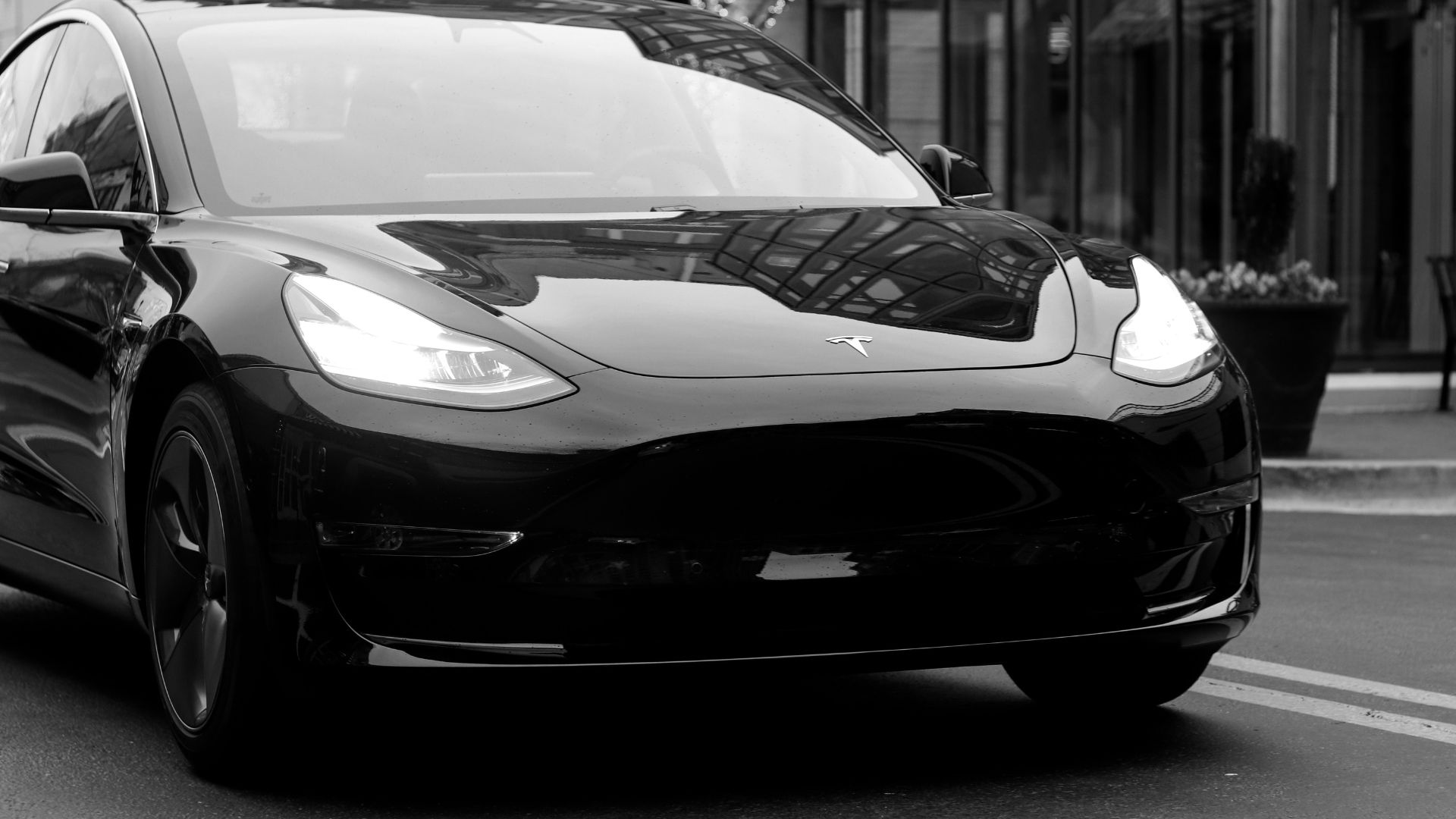
Control arms and links, though minor components, have been at the center of Tesla’s suspension problems, as per the investigation conducted by Reuters.
These failures have been persistent, with repeated redesigns failing to resolve the issue. The frequent failure of these critical parts, often in new vehicles, has led to customer dissatisfaction and raised concerns about the safety and reliability of Tesla vehicles.
Regulatory Scrutiny of Autopilot and Full Self-Driving Features
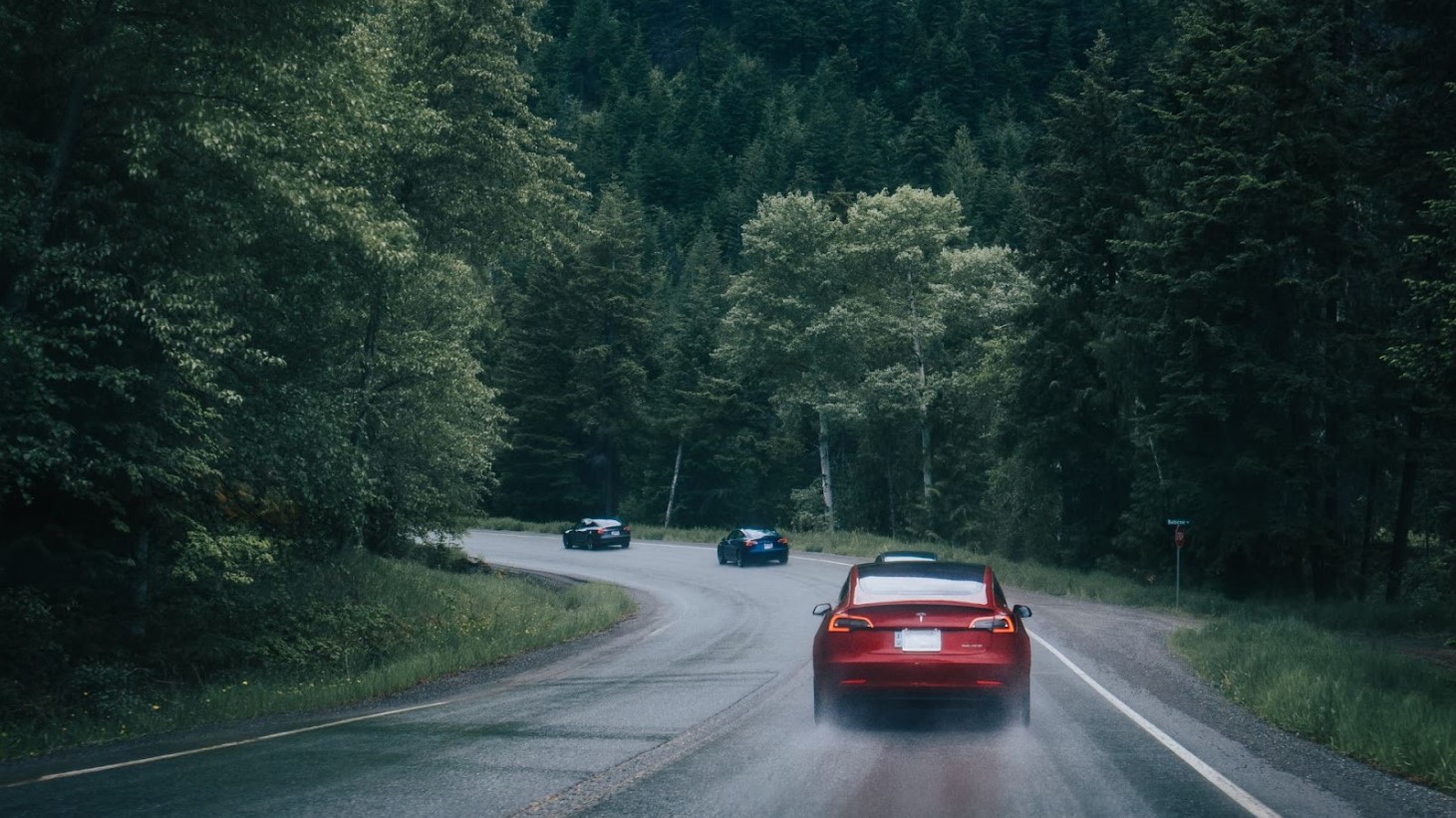
Tesla’s Autopilot and beta Full Self-Driving features have also been under regulatory scrutiny.
The NHTSA identified issues with Tesla’s system for monitoring drivers using these features, leading to an over-the-air update by Tesla.
A Range of Quality Issues Reported by Owners
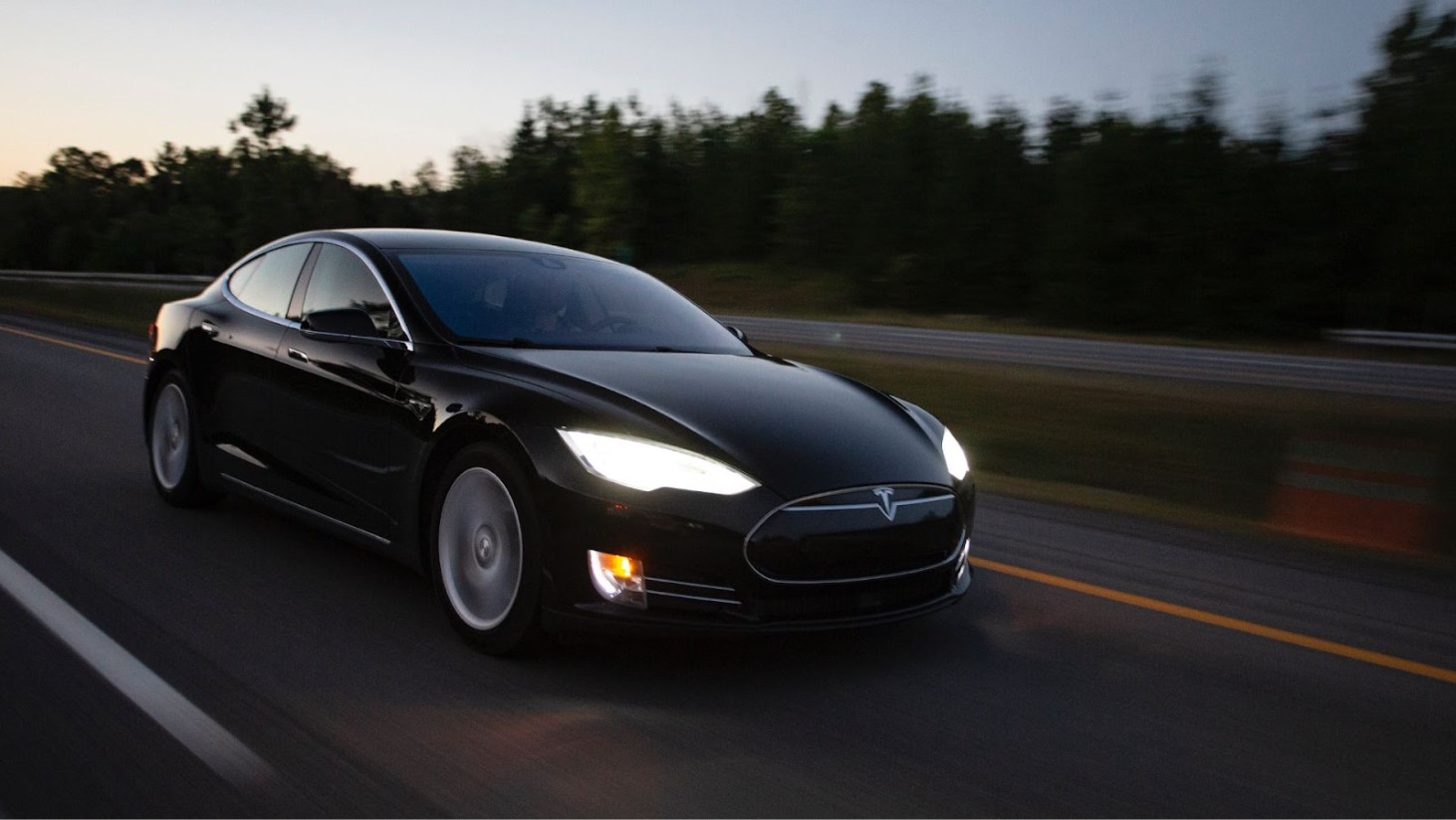
Tesla owners have reported various quality control issues over the years, including panel gaps, uneven paint jobs, and problems at Tesla’s service centers.
These reports, collected from different sources, paint a picture of a company struggling to maintain consistent quality standards across its range of electric vehicles.
International Impact and Recall Resistance
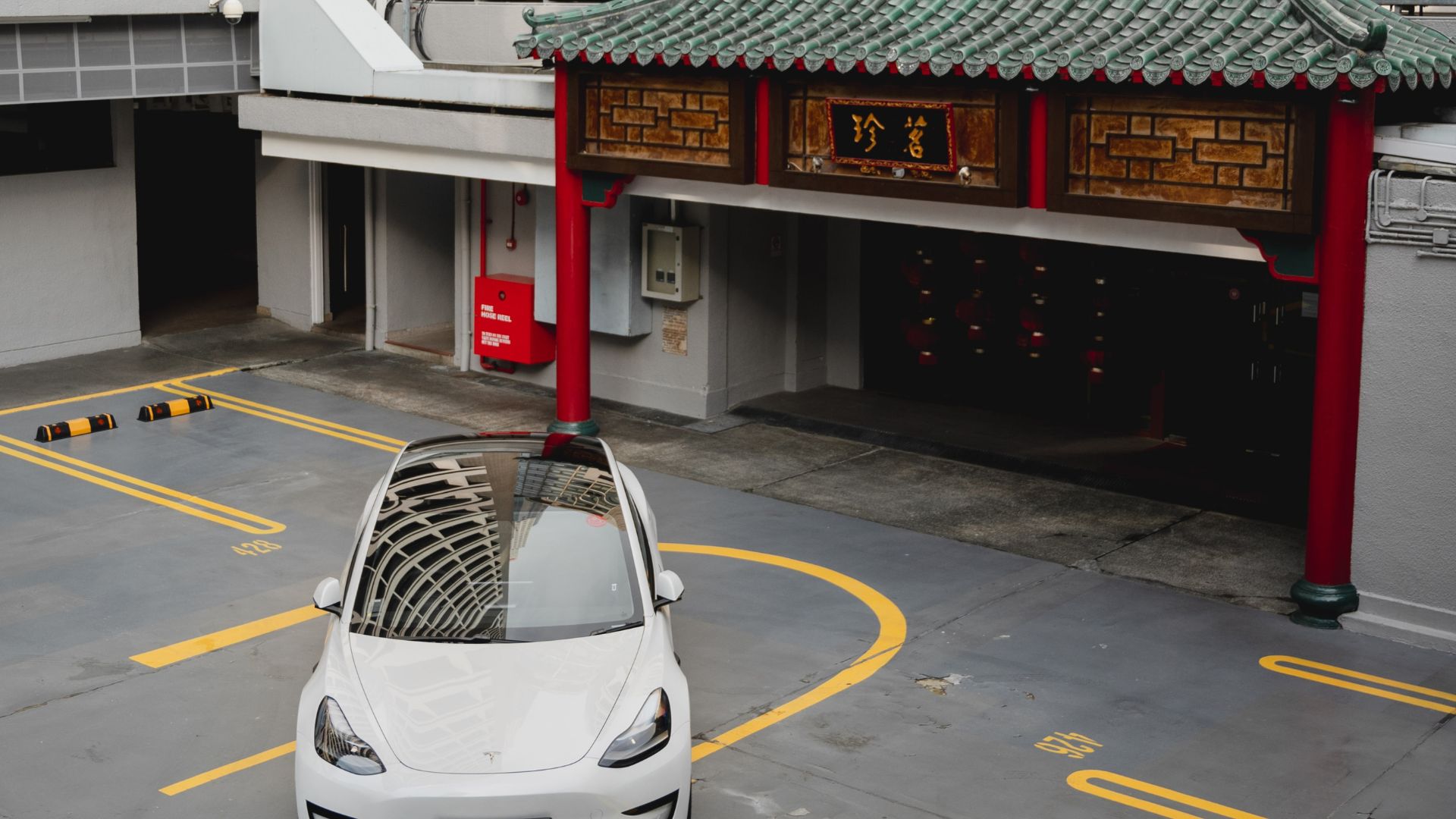
Reuters revealed that the suspension issues experienced by Tesla customers are not confined to the United States. In China, similar problems led to a recall due to regulatory pressure.
However, Tesla resisted recalling the same parts in the U.S. and Europe, blaming driver abuse instead. This inconsistency in response to similar issues across different regions underscores the global impact of Tesla’s defective parts.
Legal Challenges and Limited Recalls in the U.S.
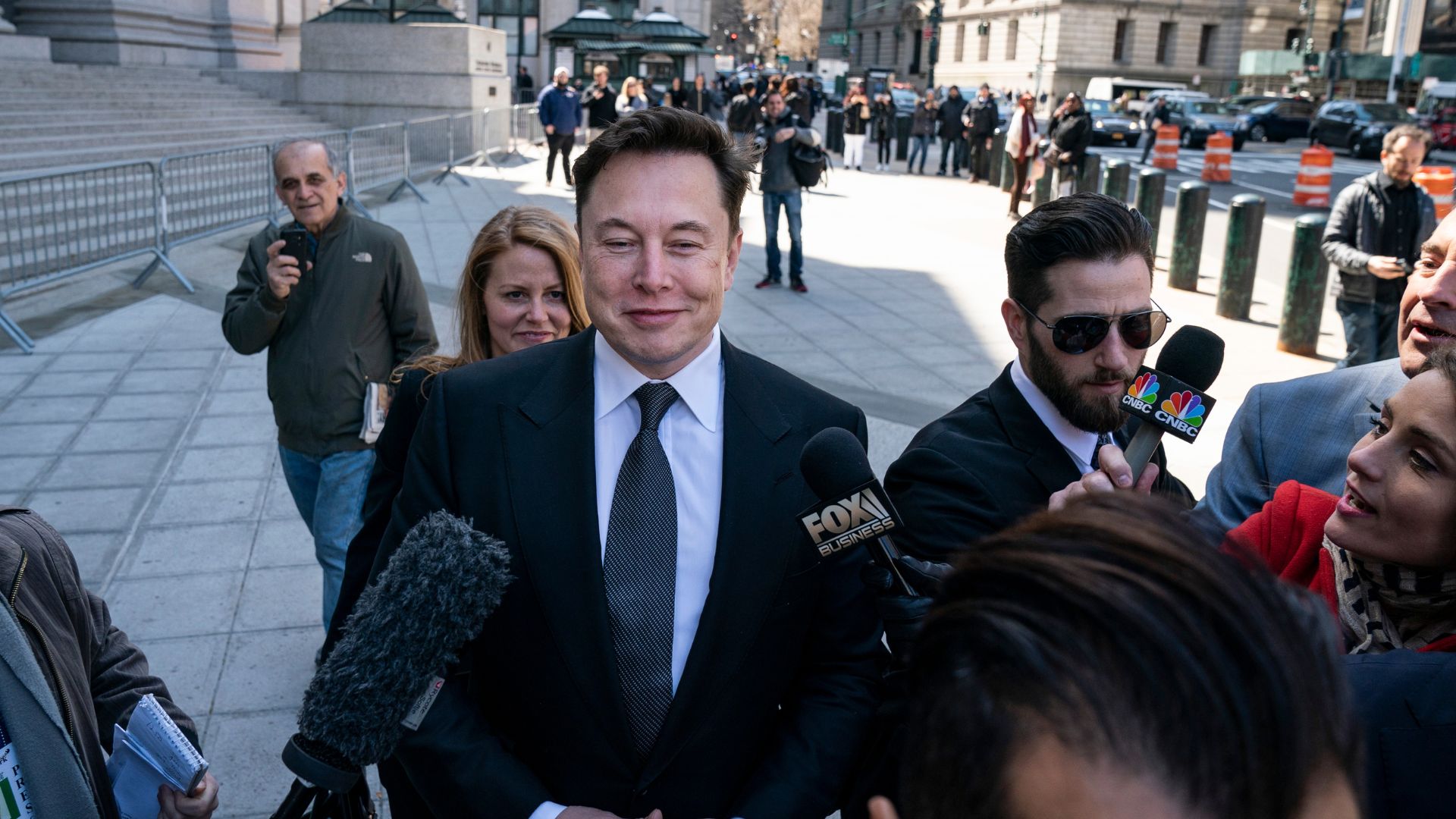
Tesla has faced legal challenges due to these suspension issues, including a class-action lawsuit alleging the company was aware of defects but refused to cover repair costs, as stated by Reuters.
However, the lawsuit faced setbacks. In terms of recalls, Tesla’s actions in the U.S. have been relatively limited, with most affecting a small number of vehicles, despite evidence of widespread issues.
The Impact on Tesla’s Reputation
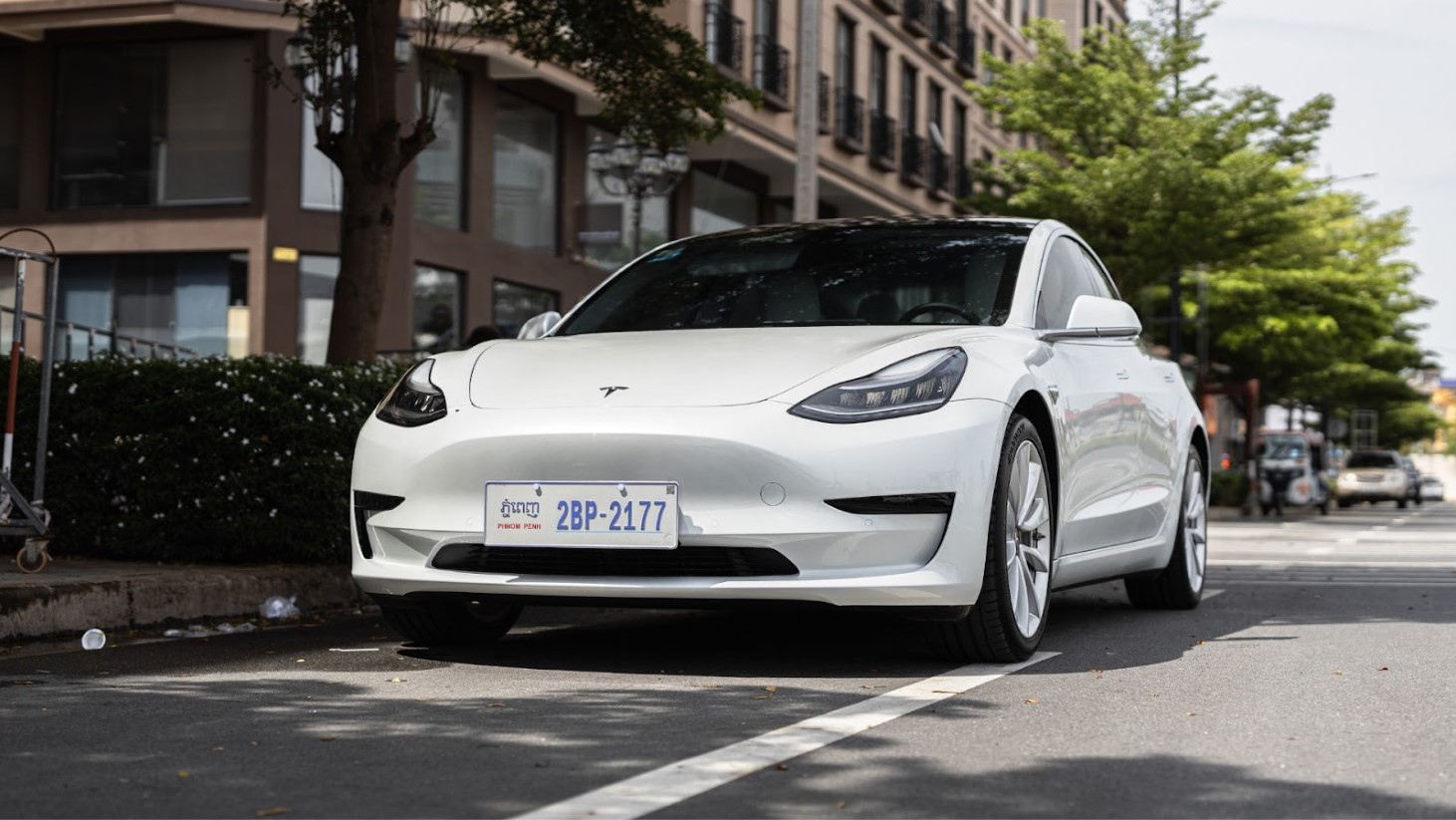
As these incidents and reports continue to surface, Tesla’s reputation for innovative electric vehicles is being challenged by concerns over quality and safety.
How the company addresses these issues will be crucial in maintaining customer trust and upholding its position in the automotive industry.
The Price of Pioneering Technology
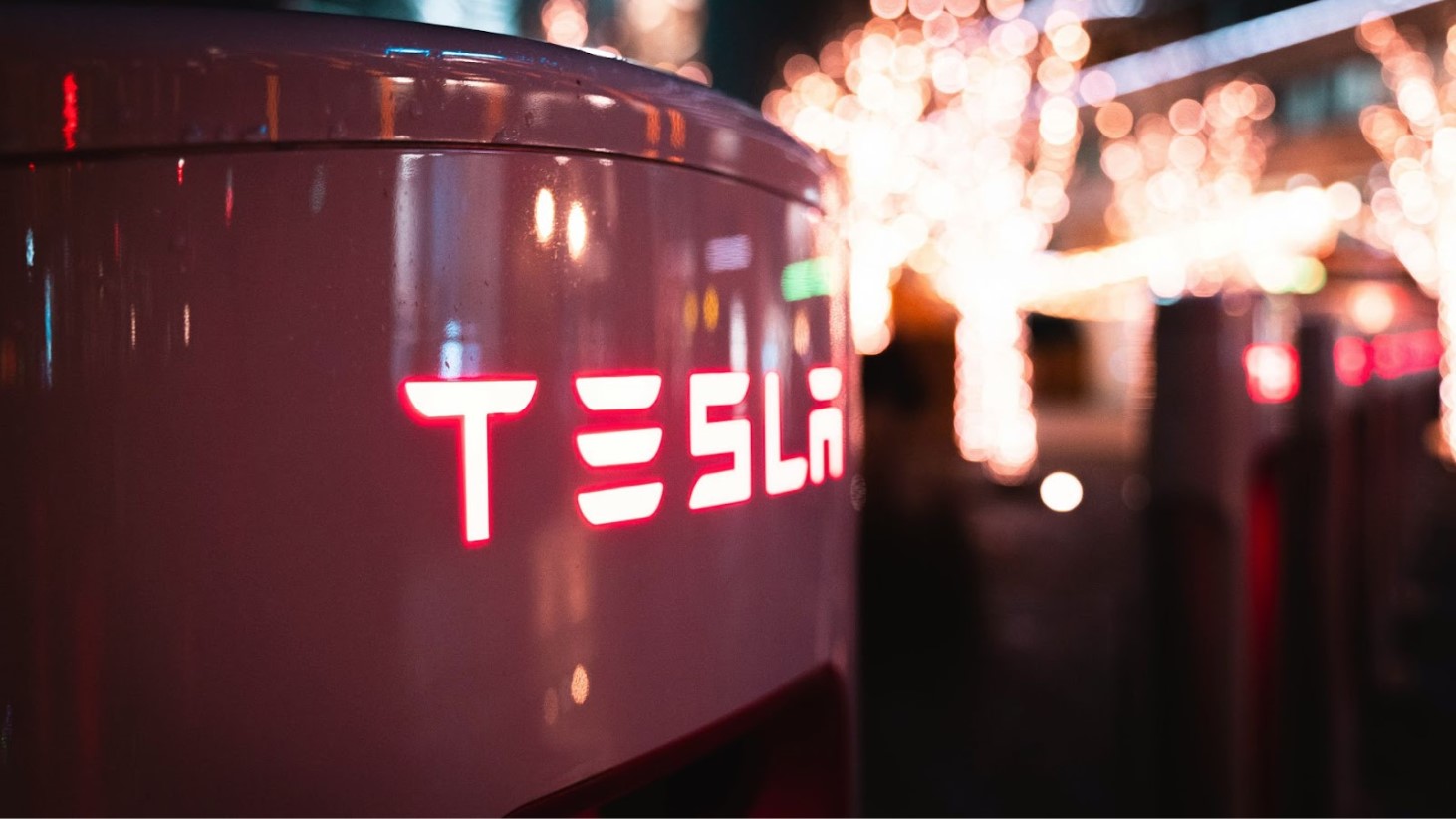
Owning a Tesla is often seen as a commitment to cutting-edge automotive technology.
However, these recent reports suggest that embracing such technology can come with unanticipated challenges and reliability issues. For Tesla, balancing innovation with quality assurance is becoming increasingly important.
The Financial Implications of Tesla’s Repair Policies
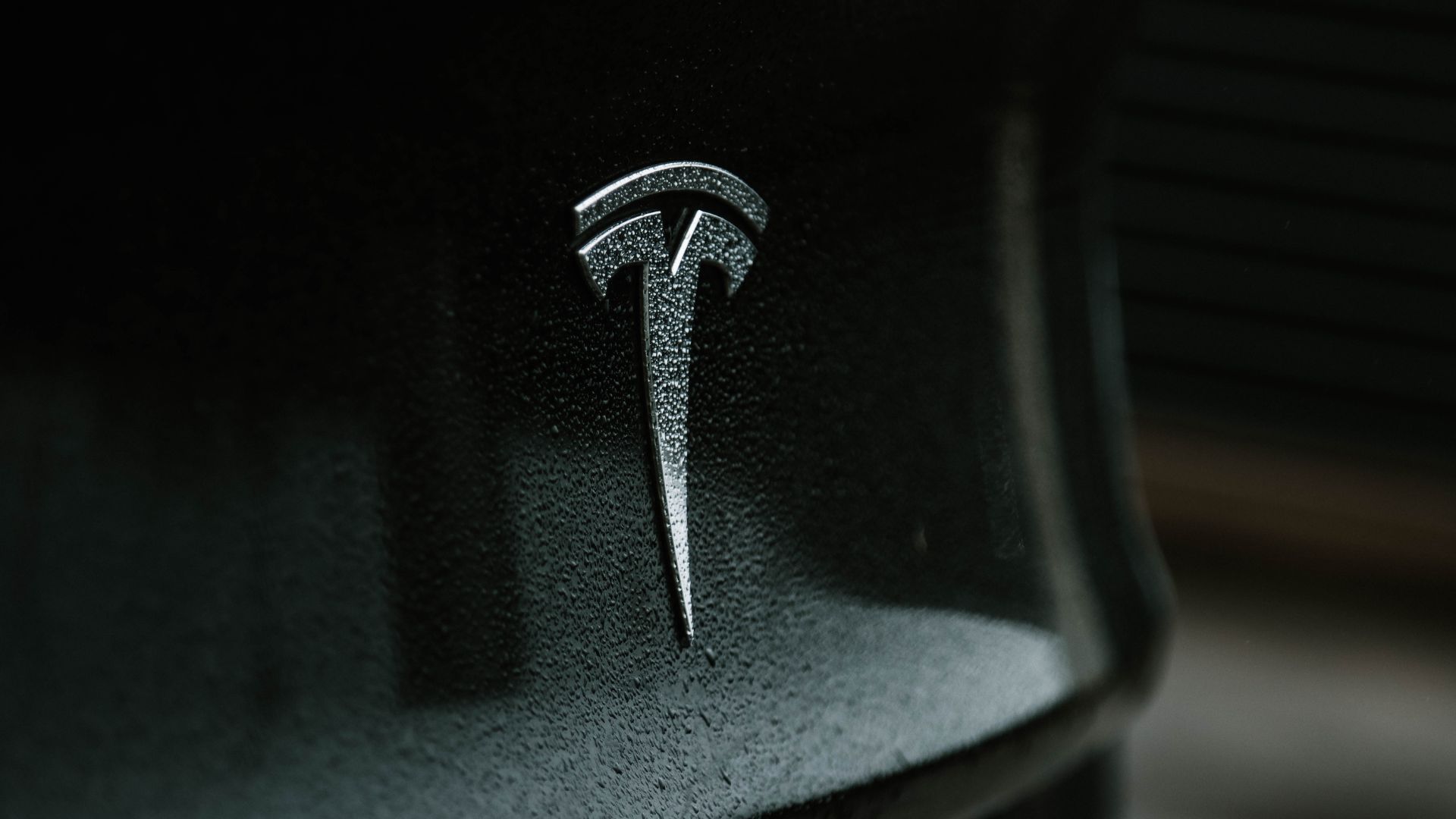
Reuters explains how Tesla’s efforts to minimize warranty and goodwill repair costs have had significant financial implications for customers. Many U.S. customers with out-of-warranty cars ended up paying substantial amounts for repairs.
This approach of cost minimization, especially in light of similar issues being addressed differently in China, highlights the economic burden placed on Tesla owners facing these defects.
Driver’s Near-Miss with Tesla’s Power Steering Failure
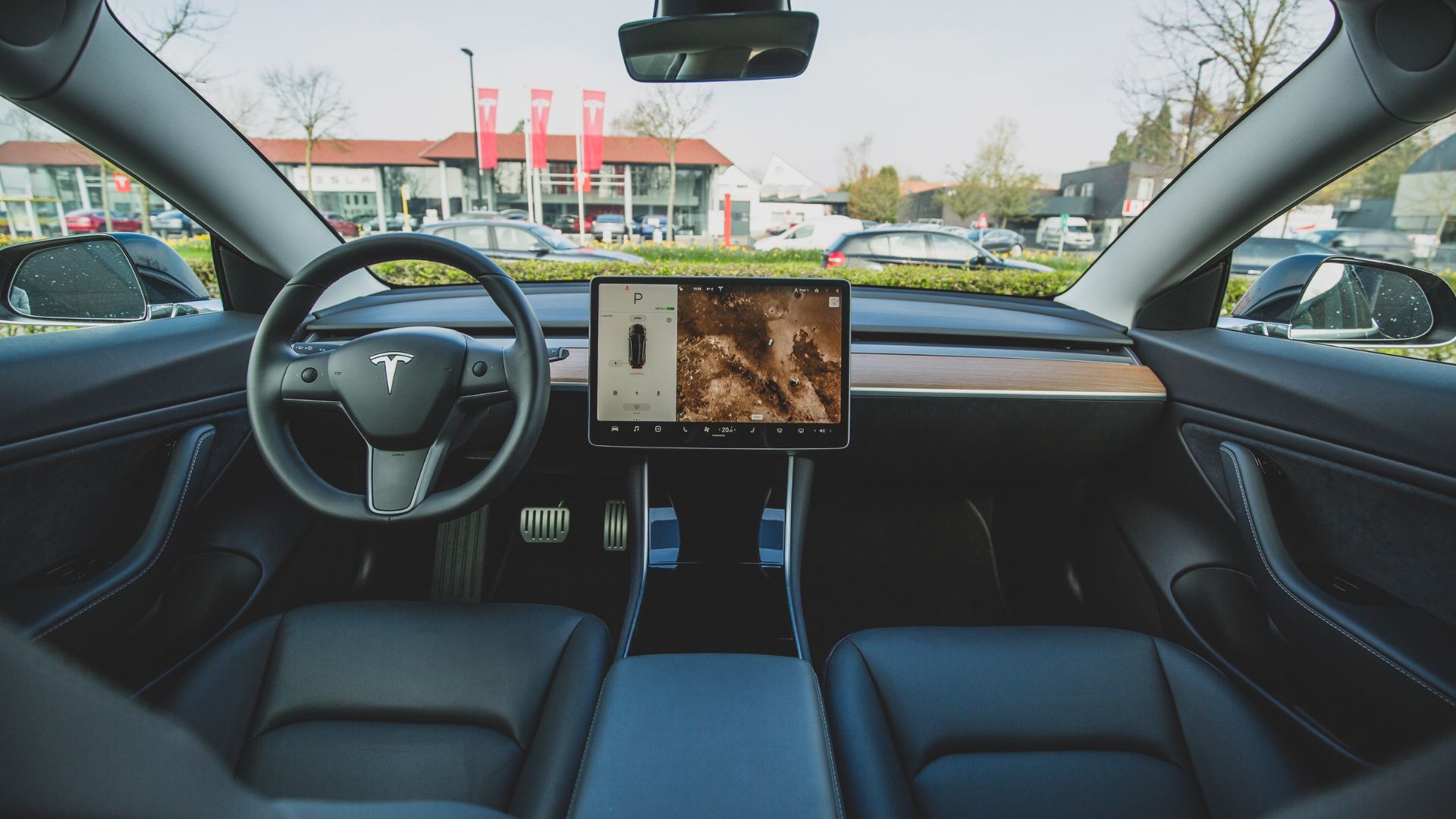
The investigation by Reuters also details the frightening story of Jamie Minshall, a Tesla Model Y owner, who faced a harrowing incident just two months into ownership. His car unexpectedly jerked, accompanied by a dashboard warning of power steering loss, making steering challenging.
“It tried to kill me,” Minshall expressed, recalling how he narrowly avoided a ditch. “It was pretty terrifying,” he shared.
Safety Risks in High-Speed Scenarios
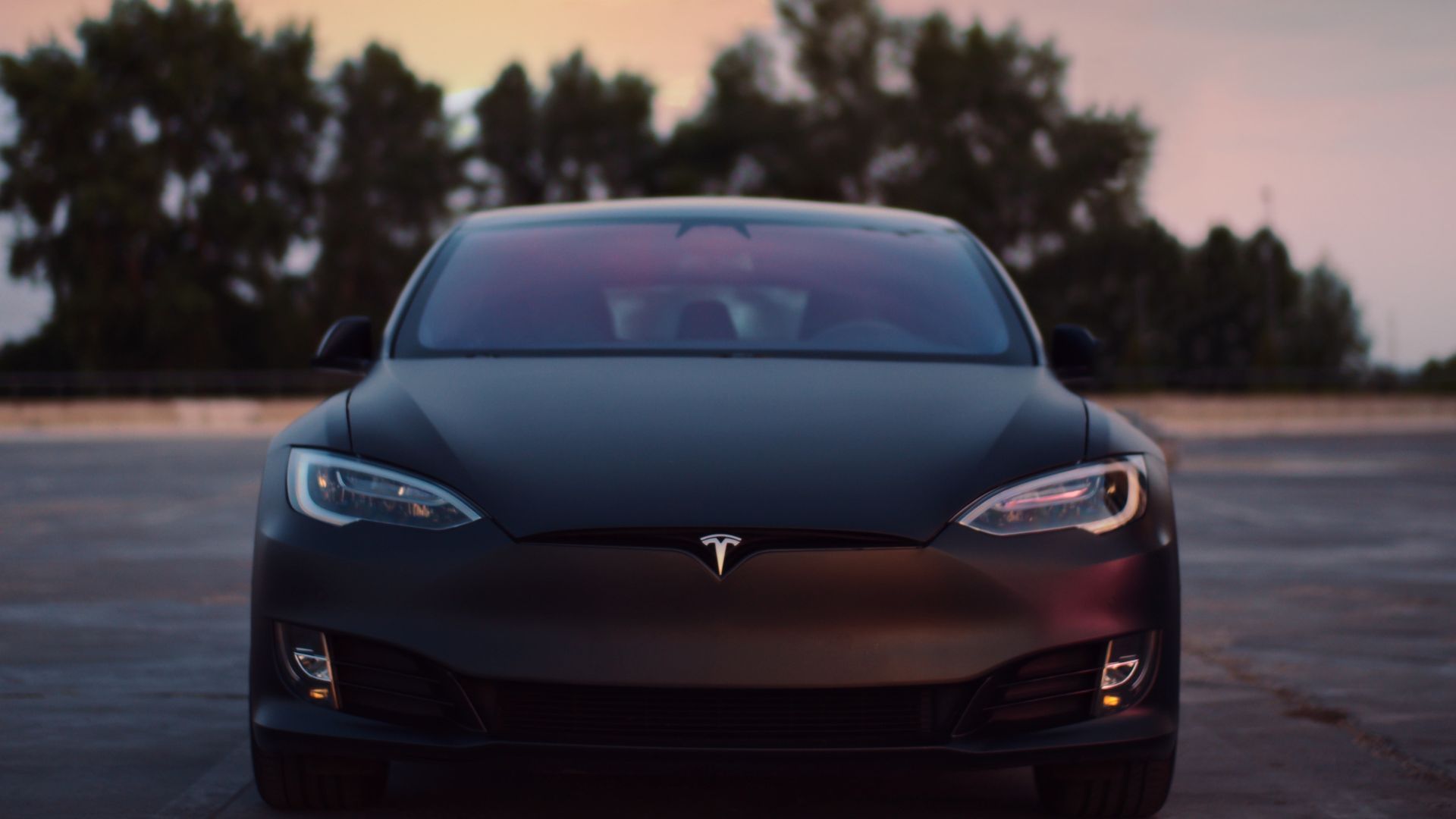
The defects in Tesla’s vehicles aren’t just about inconvenience or repair costs; they pose real safety risks. Instances of sudden power-steering failures, like the one experienced by Jamie Minshall in his 2023 Model Y, illustrate the potential for dangerous situations.
These malfunctions, especially at high speeds, significantly increase the risk of accidents, raising serious safety concerns for Tesla drivers.
Tesla’s Future: Addressing Quality Control Issues
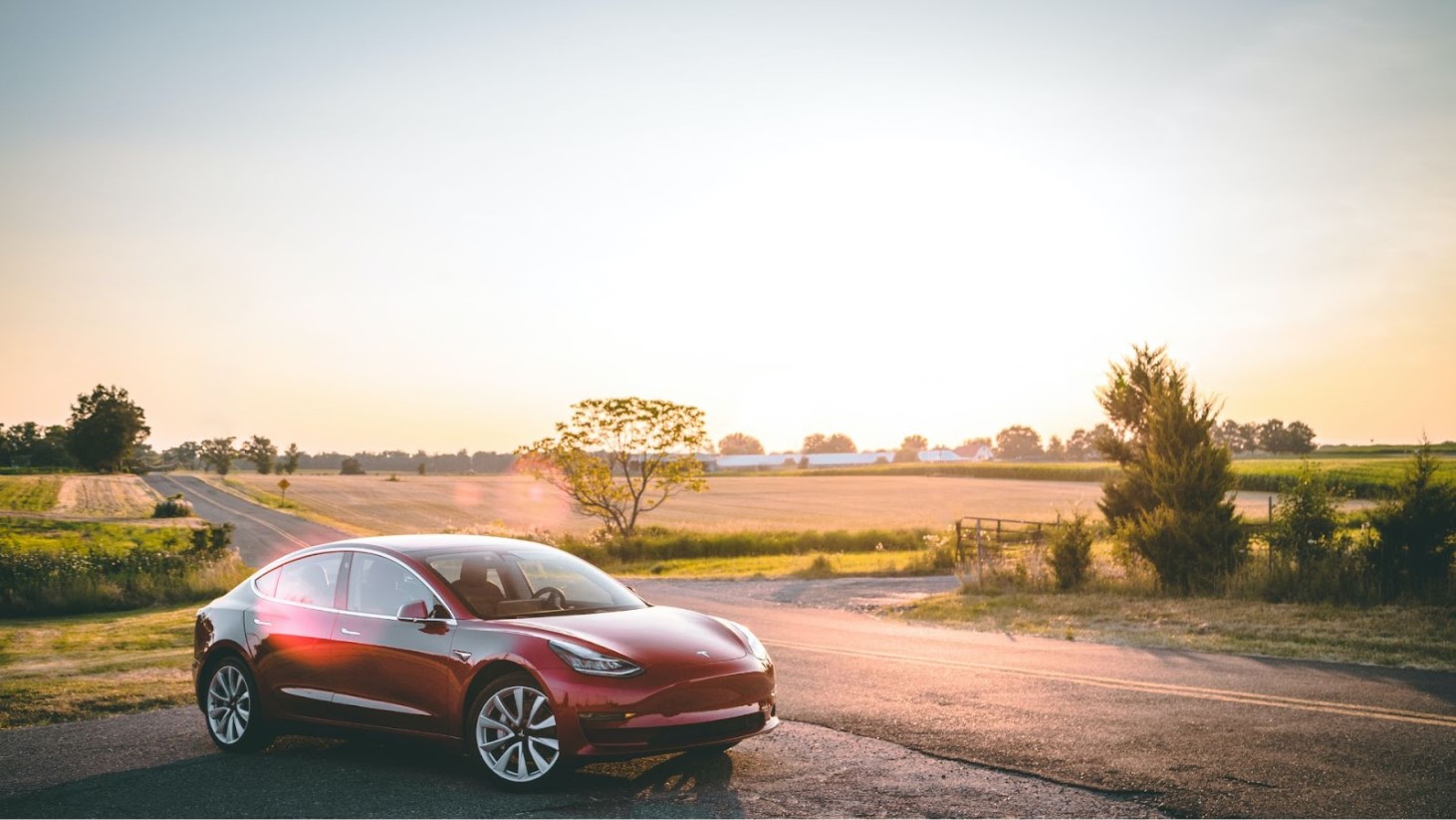
The focus now shifts to how Tesla plans to address these recurring quality control issues. With a growing number of customer complaints and regulatory scrutiny, the company’s response will be critical in determining its future success and the trust of its customer base.
The resolution of these issues will be a key factor in Tesla’s ongoing journey as a leader in the electric vehicle market.